Foreword
The purpose of describing this hypothetical company is to use it as reference to explore ideas on how to improve the Automation Systems of a manufacturing company using Intelligent Environments paradigm.Note: The company information is hypothetical but based on our experience of a typical medium size manufacturing company from our region. The names of this case study are of course also fictitious.
Introduction
Pedro the director of ACME hired FUTURA a consulting firm specialized on Automation Systems. Jorge a senior consultant from FUTURA had explained to Pedro that there are new tools derived from the field of Intelligent Environments that could be used to improve their automation systems.By Pedro’s request Jorge visited the main plant of ACME located between Leon and Silao Guanajuato to take notes on the machines, processes, infrastructure and current automation systems of this plant.
ACME headquarters offices are also located at this plant.
Jorge’s notes about ACME
Pedro had explained to Jorge that ACME has another plant about half the size of this one located in the city of Queretaro which is about an hour and a half drive from this plant. The plant in Queretaro has no administrative offices only production and some small offices for maintenance, production and support personnel. ACME has also sales offices at Mexico, Guadalajara, Monterrey and Veracruz. Each sales office has a small warehouse. There are 5 employees at each sales office including 2 regional sales agents.Jorge made a draft layout of ACME headquarters see fig. 1.
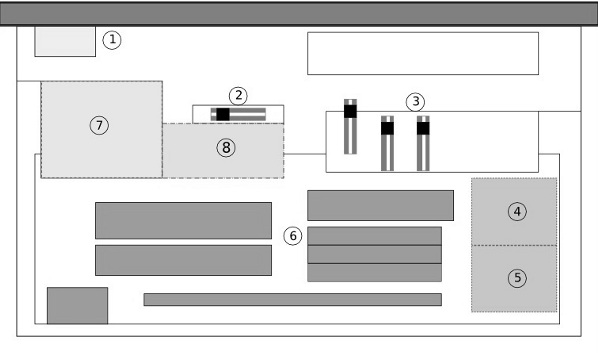
Fig 1. Plant Layout
- Main Entrance.
- Truck weighing scale.
- Truck docking stations.
- Raw material warehouse.
- Finish products warehouse.
- Production plant including machinery.
- Headquarters offices.
- Training room.
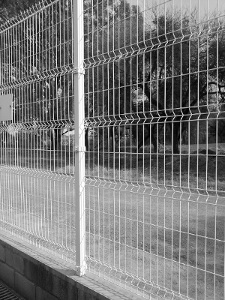
Fig. 2 Final Product
Last year ACME had sales for 700 million pesos. Their main plant has 300 employees from which 85 are office workers. Their Queretaro plant has 120 employees from which 20 are office workers.
Jorge noted that their machines have PLC's, HMI panels and speed controllers from different brands.
There is a SCADA system already in place gathering some basic information from each machine like production as parts or meters depending on the process. Temperatures and some alarms. This SCADA system is also logging the history of this information and could be presented as a list or a graph from a requested date range.
The SCADA system is of Siemens brand and to this date only the machines with Siemens PLC's are connected to this system. There are plans to integrate the rest of the machines to this system using network gateways and or monitoring stations.
ACME has an in-house developed administration system and they are in the middle of the process of implementing an ERP system. The implementation will be done in two main phases, first phase will be administration and it is almost ready. They are already running simulations for this phase. The second phase will be production. In the future they are planning to implement a MES system that will integrate the information from the SCADA system into the ERP.
As a side note they evaluated an OSS vs. a commercial solution when selecting their ERP. They decided to purchase a commercial solution because the consultants had more experience and they could help the company not just implement the ERP but also to adopt best practices.
ACME has a training room where they keep videos to train operators on their different machines.
Jorge spoke with Ruben a machine operator that has been working at ACME for two years. Ruben told Jorge about an unfortunate experience a few weeks after he had started to work at ACME, the machine had presented an unusual condition that was not covered in the training video and because of a bad corrective action an important part of the machine broke, they had to wait 2 weeks for a replacement part to arrive. Not only did they lost the profits for the lost production but they had to delay some orders and those customers were forced to buy this product from our competition.
Jorge also spoke to Adriana that is in charge of procurement for maintenance parts. Adriana told Jorge that they have spare parts for 80% by part number of the special parts with long lead time to acquire, this usually means more than a week. There are parts that have a 4 to 6 weeks acquisition lead time. Her concern is that when they need to use one of the spares that part number is no longer available on their stock and the risk of stopping production for such a long period makes them very nervous.
Maintenance division has a mechanical and electrical department, they do use outsourcing to do some major repairs. They sometimes do complete overhauls on some machines and design and implement machine modifications and upgrades to better serve their needs. The problem is that this division has 40 employees which is a big expense for the company. Part of the justification of having such a large in-house operation is to avoid having many people from the outside observing their operations and the improvements that they have made to their machines or their special manufacturing processes.
The plant also has a video surveillance system with 10 fixed cameras and 4 robotic cameras. This cameras cover almost all areas of the plant including exterior and interior. All cameras are wired IP cameras. This cameras are connected to a video recorder.
Additional information about this ACME plant:
Processes:
- Wire drawing machine to get the 1/2 inch raw wire to a smaller diameter.
- Steel wire galvanizing line.
- Wire mesh welding machines.
- Crimped Wire Mesh Machine.
- Diamond Wire Mesh (Chain Link Fence) Machine.
- Barbed wire machine.
Equipment:
- Air compressors.
- 2 overhead cranes covering all the plant.
- Truck weighing scale.
Office standard equipment:
- AC units.
- Water pressure system.
Site:
- Phone switch
- IT Servers.
- Video surveillance recorder.
Jorge’s Preliminary assessment
Jorge explained to Pedro that he has detected several areas where there is an opportunity to improve. He clarifies that not all recommendations will be using Intelligent Environments tools, because some of them will only set up the foundations for more advanced solutions to take place.First of all he approves on the ongoing plans for ERP implementation including the MES module. He also approves the plans to connect the SCADA system to the machines that are currently not included, he also points out that it is advisable to include more information on the currently networked machines for example data from other existing sensors and data from the PLC like set-points, etc. He explains to Jorge that this initiatives will be used as part of the infrastructure needed to implement more advanced Intelligent Environment solutions.
There are however still gaps that need to be filled for the infrastructure to be complete. An ID system for all ACME stake holders will be needed, this system should be able to identify employees, clients and suppliers. A b2b and and e-commerce solution that will use the ID system will be also desirable.
For employees a RFID or cellular ID system will be required. This system will control the places and times where each employee has access within the premises. Video surveillance systems from both plants should be synchronized between them and also to an off-site service provider so that in case of a sinister there will always be a backup of all the information. This applies also to all the databases an system information for example ERP, SCADA system, etc.
Intelligent Environment tools that could be used taking advantage of the baseline infrastructure that we have setup.
- Context sensitive reports from the machine operators.
- Machine and infrastructure documentation available in a digital and distributed format to the personal that has enough privileges to access and or modify it.
- Combining the 2 previous points to access documentation of any machine part using augmented reality using for example a tablet with integrated camera.
- Improve the training videos for the machine operators with augmented reality simulations of the machines. This will save energy and also avoid damaging the actual machine while a new operator is being trained.
Workshop Exercise
Jorge will now setup a meeting with a multidisciplinary group of consultants that FUTURA uses, first to validate a preliminary proposal and detect new areas of opportunities for their customers using the information that the consultant in charge of the case has gathered.In this case the workshop participants will play the role of the multidisciplinary consultants so you will be expected to read and discuss the study case. Make comments on the merits of the preliminary assessment ?and then make a brainstorming session to explore new areas of improvement for ACME.